It’s high time the fragmented Indian manufacturing industry techs up to meet Industry 4.0 demands head on.
In the highly fragmented manufacturing industry in India, the process of finding the right vendor and figuring out the manufacturing process, fair prices etc. is often tedious, time-consuming and inefficient.
Read more: How Industry 4.0 is the way forward for futuristic smart manufacturing
According to IBEF numbers, the appliances and consumer electronics market in India is projected to grow to US$21.18 billion by 2025, and a NITI Aayog report and RMI India say the electric vehicles financing industry in India is projected to grow to ~ US$50 billion by 2030.
To meet this demand in the future, India needs to infuse its supply chain, shop floor management or employee management processes with IoT, automation, cloud, and HRM systems.
While the manufacturing industry in India is overhauling itself by becoming digitised, how much has it achieved?
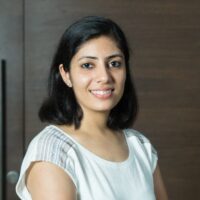
Sonam Motwani
Large and forward looking enterprises have adopted digitisation and are rapidly integrating their system while smaller enterprises are gradually adopting this concept
The Tech Panda spoke to Sonam Motwani, Founder and CEO of Karkhana.io, an on-demand, B2B manufacturing platform, who predicts the digitisation trends to be expected in the manufacturing industry in India in 2022.
Motwani says that in the manufacturing industry, the state of digitisation varies depending on the size of the organisation and the sector.
“Generally, in our experience, we have seen large and forward looking enterprises have adopted digitisation and are rapidly integrating their system while smaller enterprises are gradually adopting this concept. Overall, around US$5-6 billion have been spent on digitalisation initiatives by the manufacturing industry,” she reveals.
Globally, companies have spent over US$900 billion on industry 4.0 initiatives, and hence India is comparatively a much smaller market. The US, for example, is way ahead. Names like Tesla, Amazon, and Henkel are investing in greenfield plants, expansions, and digitisation. India hasn’t yet embraced the shift to on demand manufacturing.
“On-demand manufacturing is a new concept across the world, and in India as well. Hence, we are yet to see a shift to on-demand manufacturing in India,” she says.
“However, we are seeing a broader acceptance and implementation of Industry 4.0 concept, which augurs well for proponents of on-demand manufacturing,” she adds hopefully.
Manufacturing trends for 2022
As India gears up for Industry 4.0, demand is going to pour in, and we will see several trends in digitisation in the manufacturing industry, predicts Motwani.
Digital-twin based solutions
Companies are looking to use digital-twin based solutions to optimise resources. Motwani predicts that industries are going to spend US$4.6 billion globally on digital-twin based solutions.
Industries are going to spend US$4.6 billion globally on digital-twin based solutions
A digital twin is a virtual model of a physical asset like factory or parts of a product. It allows companies to optimise resources as companies perform simulation and testing in a virtual environment before using actual resources.
Only last week, Kraft Heinz and Microsoft joined hands to create digital twins for Kraft Heinz’ 34 owned manufacturing facilities in North America to help test and perfect solutions and processes before applying them on the plant floor.
Data Science
2022 will also see the usage of data science to enable planned maintenance to increase cost savings.
“Manufacturing firms are using data science to improve their machine’s life. They are installing sensors in machine to detect failures in advance,” reveals Motwani.
Manufacturing firms are using data science to improve their machine’s life… Such kind of planned maintenance can lead to 12% cost savings to the manufacturing companies
The sensors collect data and history of the machine. And this data is used by manufacturers to figure out the root cause of failure. Then, appropriate steps are taken in advance to increase the machine’s life.
“Such kind of planned maintenance can lead to 12% cost savings to the manufacturing companies,” she adds.
Industry 4.0 skills
Manufacturers will partner with institutions to build employees skilled in Industry 4.0 technologies.
One of the biggest challenges is to attract and retain new talent, especially Millennials and Gen-Z. Manufacturers are thus forming relationships with technical education institutions to develop their employees of the future
“Soon, in the future, manufacturers will shift to Industry 4.0 so as to maintain its existence and to remain competitive in the market. Since 2020, the manufacturing industry has experienced the shortage of skilled labour and one of the biggest challenges is to attract and retain new talent, especially Millennials and Gen-Z. Manufacturers are thus forming relationships with technical education institutions to develop their employees of the future,” she says.
The need for a tech savvy manufacturing workforce has been reiterated often.
Read more: Robot tax: Innovation vs. social adaption of automation
With the manufacturing sector contributing to over 14.5% of the country’s GDP, expected to create 100 million new jobs and touch the US$1 trillion mark by 2025, there is a rise in the need for bettering cognitive, social, behavioural, and functional skills to cater to a changing market.
As a new workforce interacts with emerging technology, there is a need to sharpen social, behavioural, and cognitive skills like crisis management, resilience, interpersonal communication, quick decision making, and critical thinking.